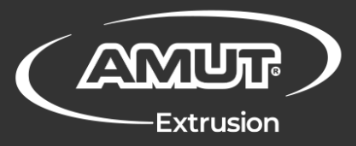
AMUT Sheet, Foil and Cast Film Extrusion Systems
AMUT designs and builds extrusion systems for sheet, foil, and cast film processing—tailored for packaging, industrial, and custom applications.



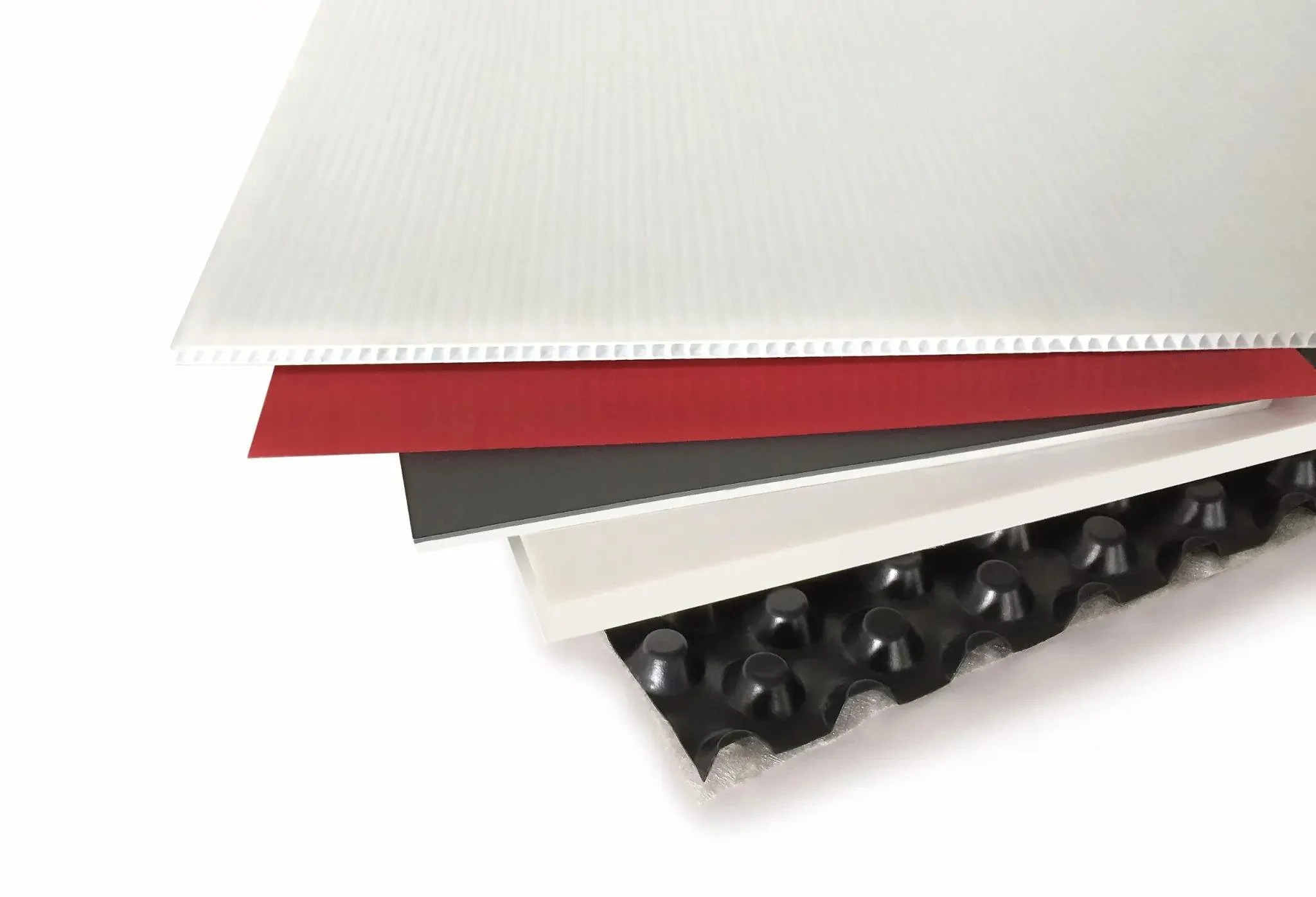
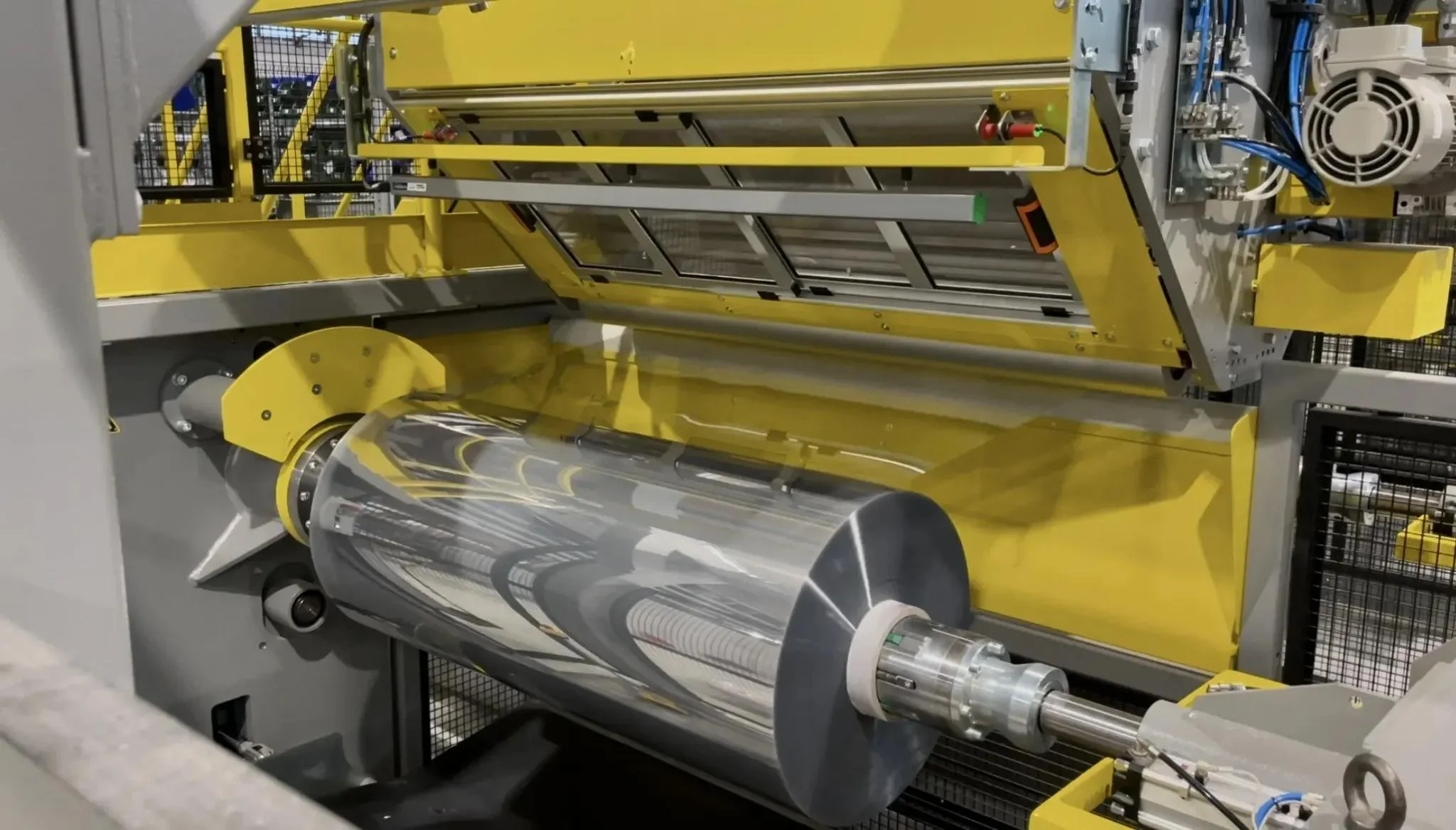
Differences Between Thermoplastic Foil, Cast Film, and Sheet Extrusion
The terms may vary worldwide, but no matter where you are, AMUT delivers advanced technology and proven reliability for producing all three. The difference between the three is the thickness, and in many cases, the number of rolls used in each process. Otherwise, they have much in common, as all are made using adjustable lip flat dies. Generally speaking, in the United States of America, the terms of difference are as follows:
Cast Film: less than 0.010 inch (ten-thousandths)
Sheet: 0.010 inch or greater
Foils: typically refers to thin cast film, 150 microns and up
Benefits of AMUT Sheet, Foil, and Cast Film Extrusion Systems
Plastic Sheet, Film, and Foil Extrusion Systems custom built to suit your needs
We supply complete extrusion systems for producing plastic foils, cast films, and sheets. Built for performance and reliability, these systems are designed to handle a broad range of thermoplastic resins across a variety of end-use sectors in the United States.
Drawing on over five decades of experience in flat-die extrusion, our solutions support widths from 16 inches up to 130 inches (400 to 3300 mm) and thicknesses starting at 6 mils (150 microns), extending to multi-inch structural panels. Learn more about AMUT’s global engineering capabilities and company history on our AMUT corporate overview page.
Applications for AMUT Sheet, Foil, and Cast Film Extrusion Lines
Food Packaging Applications
Extruded sheet for thermoformed food containers, available with or without barrier layers. Structures may be laminated or co-extruded to maintain product freshness, and surfaces can be prepared for printing or metallizing. Options available for use in high-speed form-fill-seal lines.
Typical materials: PET, PS, PE, PP, EVA, EVOH.
Retail and Medical Blister Packs
Films for thermoformed consumer packaging and pharmaceutical blister packs. Available with surface treatments that enable heat sealing or bonding.
Typical materials: PET, PVC, PP.
Stationery and Premium Folding Cartons
Extruded plastic for binders, folders, packaging sleeves, and specialty retail boxes. Offered in single- and multi-layer configurations with optional embossing and print treatment. Supplied in sheet or ream format.
Typical materials: PET, PP, PVC.
Residential and Kitchen Furniture Boards
Sheets for cabinet doors, drawer fronts, and edge bands. These may feature woodgrain embossing, primer coatings, and printed finishes cured under UV light.
Typical materials: ABS, PMMA, PVC, PP.
Appliance and Bathroom Component Manufacturing
Sheets designed for thermoformed refrigerator liners, tub surrounds, shower bases, and vanity components. Engineered for gloss retention, chemical resistance, and compatibility with foam injection.
Typical materials: PS (HiPS and GPPS), ABS, PMMA.
Medical Fluid Delivery Products
Safe, non-toxic film used in production of IV, dialysis, and blood bags. Available with anti-block finishes to withstand autoclave sterilization cycles.
Typical materials: PVC, PP.
Corrugated Plastic Sheet (Multi-Wall Panels)
Extruded polypropylene and polycarbonate panels for U.S. signage, printing, and construction markets. Available in single- and multi-wall formats.
Typical materials: PP (Cartonplast), PC.
Automotive Interior and Structural Components
Sound-dampening, reinforced, and co-extruded sheets for vehicle trunk liners, door panels, and engine bay insulation. Available with nonwoven or textile backings.
Typical materials: PP, TPO, PVC.
Custom and Industrial Solutions
Corrugated sheets with foam layers for bulk packaging (e.g., coils, pipes)
While AMUT sheet extrusion lines are ideal for producing flat thermoplastic panels, our edgebanding extrusion lines specialize in creating decorative edging strips used in furniture and cabinetry production.
Transparent GPPS sheets for hobby, signage, and retail display
Fluoropolymer films for seals and chemical-resistant barriers
Synthetic leather and partitioning films for industrial and commercial use
Typical materials: LDPE foam, GPPS, PFA, PVDF, flexible PVC
Please see the PDF literature and videos below for expanded details. EXTRUDAMERICA proudly represents AMUT extrusion systems across the Northeast Census Region and Mid-Atlantic Census Region. — see our sales territory coverage for more information.
Contact EXTRUDAMERICA now for further information or a quotation!
Extrusion line to produce mono layer low thickness PP foil with Air Blade System
SINGLE SCREW EXTRUDER 52 L/D + EASY FEED SYSTEM Output 1.000 kg/h Innovative feeding and extrusion concept based on screw 52 L/D developed by AMUT R&D Division to process up to 100% low thickness re-grind material, with NO production decreasing. Screw configuration for excellent action in melting, sharing and mixing all thermoplastic materials used in the thermoforming phase. Perfect flow of light and heavy re-grind materials: • bulk density rate less than 200 kg/m³ - skeleton grinding thickness down to 0.
“Bottle to Packaging” direct process
We are proud of our contribution to our customers' successful plans, to meet their sustainable packaging objectives by producing eco-friendly egg trays. At Hickman’s Family Farm, you may assist in how post-consumer bottles are transformed into a valuable resource through AMUT-EREMA's “Bottle to Packaging” direct process. Thanks to this proven technology, the flakes resulting from the treatment are 100% food contact compliant and meet #FDA regulations and #EFSA guidelines. The sheet produced from the high-quality flakes will be thermoformed into egg trays.
EXTRUSION LINE BOTTLE TO PACKAGING
r-PET Sheet - Direct process From 100% post-consumer PET bottle flakes to food grade single layer sheet NO IV DROP DURING THE PROCESS FDA and EFSA approval for food contact application High-quality PET sheet produced using 100% bottle flakes from post-consumer waste with FDA and EFSA certification. The system features a decontamination/dehumidification process (approx. one hour time) which totally extracts the volatile contaminants still present in the flakes, thus making the sheet quality better than any dryerless co-rotating system.
rPET SHEET EXTRUSION LINE – BOTTLE TO PACKAGING
ANOTHER LINE TESTED AT OUR FACILITIES BEFORE SHIPMENT TO CUSTOMER! r-PET Sheet - Direct process AMUT & EREMA combined technology From 100% post consumer PET bottle flakes to food grade single layer sheet Final Product: • Net Width = 1.600mm (62”) • Thickness Range = from 0,15mm to 1,5mm (12th to 60th) • 1.600 to 1.800 kg/h High V viscosity level NO IV DROP DURING THE PROCESS FDA and EFSA approval for food contact application ADVANTAGES OF AMUT-EREMA TECHNOLOGY - High-quality PET sheet produced using 100% bottle flakes from post-consume with FDA and EFSA certification.
EXTRUSION LINE BOTTLE TO PACKAGING
EXTRUSION LINE BOTTLE TO PACKAGING r-PET Sheet - Direct process AMUT & EREMA combined technology From 100% post-consumer PET bottle flakes to food grade single layer sheet NO IV DROP DURING THE PROCESS FDA and EFSA approval for food contact application ADVANTAGES OF AMUT-EREMA TECHNOLOGY - High-quality PET sheet produced using 100% bottle flakes from post-consumer with FDA and EFSA certification. AMUT-EREMA system features a decontamination /dehumidification process.
CO-EXTRUSION LINE FOR PET-PS-PP THERMOFORMING SHEET
CO-EXTRUSION LINE FOR PET-PS-PP THERMOFORMING SHEET Co-rotating twin screw extruder PET DRYERLESS TECHNOLOGY Technical Features: CONFIGURATION No. of Layers: 3 A - PET (virgin) - EA 60 AMUT Model B - PET (virgin and/or 100% PET Bottle Flakes and/or Regrind from Thermoforming) - EBC 90 AMUT Model A - PET (virgin) - EA 60 AMUT Model OUTPUT PET = 1.200 Kg/h PS = 1.200 kg/h PP = 1.100 kg/h USEFUL WIDTH 1.000 mm THICKNESS PET = 0.15-1.5 mm PS = 0.2-2.0 mm PP = 0.2-2.
EXTRUSION LINE FOR THE PRODUCTION OF LDPE EMBOSSED FOIL
EXTRUSION LINE FOR THE PRODUCTION OF LDPE EMBOSSED FOIL Technical Features: Output: 200 kg/h Net Width: 490 mm Thickness: smooth foil 250 µm min. embossed ropes: up to 400 µm Configuration: monolayer Application: food industry.
EXTRUSION LINE FOR ABS + PMMA or PP SHEET
EXTRUSION LINE FOR ABS + PMMA or PP SHEET Technical features: Output: up to 1000 kg/h Net Width: 700 mm Thickness: 0,3 - 3 mm Production: Monolayer PP Sheet ABS Sheet + PMMA Gloss Layer Machine configuration: EA100/40D Single Screw Extruder with venting system EA48/33D Co-Extruder – A-B-A Layers configuration Calendar with Ø 600 mm cylinders Accumulating Unit 2-shaft Winder Trims cutting unit with blades Sheet automatic cutting during roll change.
SINGLE SCREW EXTRUDER 52 L/D + EASY FEED SYSTEM
SINGLE SCREW EXTRUDER 52 L/D + EASY FEED SYSTEM Innovative feeding and extrusion concept developed by AMUT R&D Division to process up to 100% low thickness re-grind material. Screw 52 L/D = 40 + 12 40 = diameters for polymer feeding, heating and melting 12 = diameters for degassing and pushing action towards the die.
EXTRUSION LINE FOR THE PRODUCTION OF FOIL IN PS AND PP
EXTRUSION LINE FOR THE PRODUCTION OF FOIL IN PS AND PP Technical Features: Material: PS - PP Foil Thickness: 0,2 ~ 2,5 mm Net Width: 1.000 mm Extruders: EA48/33D - Layer A EA75/52D – Layer B EA48/33D - Layer C Output: 1000 Kg/h EA75 Extruder Equipped with EasyFeed® 52D for reprocessing up to 100% of grinded foil from thermoforming, without output reduction Special Feedblock designed for Layers Configuration Quick Change with running Extruders Layers Configuration: 1) A – B – A 2) C – B – C 3) A – B – C 4) C – B – A 5) A – C – B – C 6) A – C – B – A 7) A – C – B – C – A 8) C.
EXTRUSION LINE FOR THE PRODUCTION OF ABS OR PP EDGEBANDING
EXTRUSION LINE FOR THE PRODUCTION OF ABS OR PP EDGEBANDING Technical Features: Applications: furniture industry Useful width: 350 mm Thickness range: 0,4 ÷ 2 mm No. Of Layers: 1, monolayer band Finished product: Band wound-up on 1200 mm EXTRUSION UNIT: no.1 Single Screw Extruder – Model EA75/52D New Design – Dryerless execution with double venting port (ABS extrusion without drying) Line Output: up to 320 kg/h Line Speed: up to 32 m/min.
DRYERLESS TECHNOLOGY - CO-EXTRUSION LINE FOR PET-PS-PP THERMOFORMING SHEETS
CO-EXTRUSION LINE FOR PET-PS-PP THERMOFORMING SHEETS Co-rotating twin screw extruder PET DRYERLESS TECHNOLOGY CONFIGURATION No. of Layers: 3 A - PET (virgin) - EA 75 AMUT Model B - PET (virgin + regrind) - EBC 108 Model A - PET (virgin) - EA 75 AMUT Model OUTPUT PET = 750 - 1.500 Kg/h PS = 1500 kg/h PP = 1350 kg/h USEFUL WIDTH 1.200 mm (600 mm x 2) THICKNESS PET = 0.15-1.5 mm PS = 0.2-2.0 mm PP = 0.2-2.
EXTRUSION LINE FOR THE PRODUCTION OF PP & PS SHEET
EXTRUSION LINE FOR THE PRODUCTION OF PP & PS SHEET Main Features: Material = PP & PS Sheet useful width = 800 mm Configuration = monolayer Foil thickness = 0.2 -2.5 mm Output =600 kg/h for PP and 700 kg/h for PS.
EXTRUSION LINE FOR PP AND ABS SHEET FOR EDGEBANDING
EXTRUSION LINE FOR PP AND ABS SHEET FOR EDGEBANDING Application: Edgebanding for the Furniture Industry Main Features: Materials: PP and ABS Net Width: 700 mm Thickness Range: 0,3 ÷ 3 mm Layers Configuration: A-B-A; A-B; B-A; B EXTRUDERS Single-screw extruders Counter-rotating twin-screw extruders: suitable to extrude PVC/R (also in powder) and ABS - Venting system with an oversized vacuum pump - Control unit for the screw thermoregulation - Screen changer group - Melt pump on a mobile trolley for easy disassembling Co-rotating twin-screw extruders: suitable to extrude ABS.
PVC - ABS SHEET FOR THE PRODUCTION OF EDGEBANDING
PVC - ABS SHEET FOR THE PRODUCTION OF EDGEBANDING Application field: furniture fittings Plastic Materials: PVC, ABS, PP, PMMA Output: 60 ÷ 600 Kg/h Sheet length: 350; 700 mm Sheet thickness: 0,3 ÷ 3 mm Extrusion speed: 2 ÷ 20 m/min Number of layers: 1; 2 ; 3 Layers geometry: A; A-B; A-B-A Coextrusion type: ABS/ABS; PMMA/ABS EXTRUDERS Single-screw extruders Counter-rotating twin-screw extruders: suitable to extrude PVC/R (also in powder) and ABS - Venting system with an oversized vacuum pump - Control unit for the screw thermoregulation - Screen changer group - Melt pump on a mobile trolley.
EXTRUSION LINE FOR CORRUGATED PVC SHEET
EXTRUSION LINE FOR CORRUGATED PVC SHEET The corrugated PVC liner panels allow efficient roofing and cladding of several structures, thus representing an optimal solution for outdoor applications. The panels have a surface that is easy to clean/sanitize and excellent resistance to chemicals, marking, and scratching. Further, the PVC is non-flammable, rustproof, and easy to maintain. The corrugated PVC sheet produced with AMUT lines can have different geometries and a thickness range from 0.8 to 2.0 mm. The extruders are twin-screw type, series BA.
CROSS-LINKED EVA FOIL EXTRUSION LINE
CROSS-LINKED EVA FOIL EXTRUSION LINE. Especially reserved for the production of solar panels. Photovoltaics is widely developing worldwide and is mentioned as one of the most important sectors for alternative energy. AMUT has prepared a highly technological line to satisfy this special application's highest demands.
PS AND PP FOIL CO-EXTRUSION LINE
PS AND PP FOIL CO-EXTRUSION LINE FEATURES: Output: HIPS = 630 kg/h PP = 350 kg/h Useful width: 1000 mm Thickness range: PS = 0.2 - 1.8 mm PP = 0.3 - 1.8 mm Configuration: 3 Layers: A -B - A AMUT applies more than 50 years of experience in plastic sheet extrusion to offer its Customers complete and technologically advanced lines to produce foils from a wide range of thermoplastic materials, to be used for a large number of different applications.
CORRUGATED SHEET EXTRUSION LINE
CORRUGATED SHEET EXTRUSION LINE Width up to 1200 mm Raw material rigid PVC Finished product application roofing Material thickness 0.8 mm approx. Production rate 220 kg/h
PS AND PP FOIL CO-EXTRUSION LINE
PS AND PP FOIL CO-EXTRUSION LINE FEATURES: Output PS = 1.000 - 1100 kg/h PP = 1.000 kg/h Useful width 1000 mm Thickness range PS = 0.15 - 2.0 mm PP = 0.3 - 2.0 mm Configuration: A -B - A or A - B or B AMUT applies more than 50 years of experience in plastic sheet extrusion to offer its Customers complete and technologically advanced lines to produce foils from a wide range of thermoplastic materials, to be used for a large number of different applications.
POLYCARBONATE AND PMMA MULTICELL PROFILE AND CORRUGATED BOARD EXTRUSION LINE
POLYCARBONATE AND PMMA MULTICELL PROFILE AND CORRUGATED BOARD EXTRUSION LINE
4-METER HDPE DIMPLED SHEET EXTRUSION LINE
4-METER HDPE DIMPLED SHEET EXTRUSION LINE AMUT GROUP has recently manufactured and tested a plant for the production of HDPE dimpled sheet, with a net width of 4 meters, for a Russian customer, being one of the biggest producers of materials for the building sector. An important technological goal, proof of the Group's continuous investments in R&D towards ambitious projects, assuring high performances.
PET, PS & PP CO-EXTRUSION SHEET LINE
PET, PS & PP CO-EXTRUSION SHEET LINE FEATURES: Material: PET, PS or PP Structure: 5 layers Output: 1.500 to 2.000kg/h Width: 1.000 mm Thickness: from 0,15 mm to 2,00 mm AMUT has more than 50 years of experience in plastic sheet extrusion and it offers to the Customers complete and technologically advanced lines to produce foils and sheets from a wide range of thermoplastic materials, to be used for a large number of different applications.
PS & PP CO-EXTRUSION SHEET LINE
PS & PP CO-EXTRUSION SHEET LINE FEATURES Material. PS or PP Structure: 5 layers Output: 1.800 kg/h Width: 1.600mm Thickness: from 0,15 mm to 2,00 mm AMUT has more than 50 years of experience in plastic sheet extrusion and it offers to the Customers complete and technologically advanced lines to produce foils and sheets from a wide range of thermoplastic materials, to be used for a large number of different applications.
CRYSTAL CLEAR PS CO-EXTRUSION SHEET LINES
CRYSTAL CLEAR PS CO-EXTRUSION SHEETLINES - AMUT has more than 50 years of experience in plastic sheet extrusion and it offers to the Customers complete and technologically advanced lines to produce foils and sheets from a wide range of thermoplastic materials, to be used for a large number of different applications. The AMUT production range includes extrusion lines with nominal widths from 400 to 3300 mm and thicknesses from 150 microns for foils up to some centimeters for sheets or multicellular panels.